M Beauchamp
Well-known member
- Joined
- Aug 15, 2011
- Messages
- 392
- Reaction score
- 5
- Location
- Sarnia Ontario
- My Car
- 1973 light blue convertible
351c 2V
How to repair a leaking, dented gas tank.
I could have purchased a new tank for $120 plus freight.
But I wanted to see if this tank could be repaired.
The repair took 6-8 hours.
First thing is clean the fuel out of the tank and flush it until all of the fumes are gone!
Here is the tank with dents and holes.


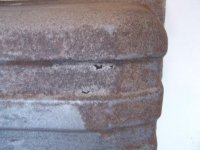
This picture you can see where the factory seam weld was.

Take a zip cut wheel and grind a grove just on the inside of the existing seam weld.
Only grind threw the top sheet metal on all four sides.
The sheet metal will turn blue as it thins out, Don't grind into the bottom sheet metal.

Take a cold chisel to separate the top sheet metal.

Pull the top and bottom apart.

Here you can see the bottom lip.

Here you can see the top lip, as well as all the rust that builds up and get in the fuel system.

Straighten the top lip out with a dolley and hammer, so it will lay flat when you weld it back together.

Blast the top and bottom pieces of the tank in and out.


The pin holes are hard to see, using a flash light behind helps locate them.


Do all your spot welding on the inside of the tank using a copper backing plate, this will save alot of grinding later.

Grind of the weld penatration the pops threw the sheet metal.


Dolley and hammer all the dents out.


Fit the Halves together.
Use vise grips to keep the sheets tight for welding.
Start at one corner and work around all four sides.
This allows you to tweek the grove back into the same location.
Tack weld about every three inches.
Grind all the tacks smooth so the seal weld can pass over them nicely.

Set the tank up on a 45 degree angle so the seam can be re-welded in a down hand position.

When welding ensure that the puddle fuses the sheet metal on both sides of the zip cut grove.
Use a slight whipping motion with the arc, backing up about 1/8" this lets you fix the weld puddle if it you loose the sheet metal on one side.
Repeat this welding on all four sides.

Here you can see the weld penatration on the back side of the seam.
Grind up any welds.

Use a polymer fuel tank liner to seal the entire interor of the tank.
This prevents rust from forming inside the tank and getting into the fuel system.
Tape up the openings.

Pour the polymer liner into the tank.

Tape the last opening and slowly rotate the tank.

Use a flash light to see that the entire interior of the tank is coated.
Pour the excess polymer out of the tank.
Let dry for 24 hrs

Paint the exterior of the tank with 2 coats of epoxy paint.
Reinstall the sending unit, vent plug and nozzle gasket.
I could have purchased a new tank for $120 plus freight.
But I wanted to see if this tank could be repaired.
The repair took 6-8 hours.
First thing is clean the fuel out of the tank and flush it until all of the fumes are gone!
Here is the tank with dents and holes.


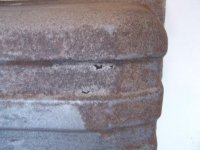
This picture you can see where the factory seam weld was.

Take a zip cut wheel and grind a grove just on the inside of the existing seam weld.
Only grind threw the top sheet metal on all four sides.
The sheet metal will turn blue as it thins out, Don't grind into the bottom sheet metal.

Take a cold chisel to separate the top sheet metal.

Pull the top and bottom apart.

Here you can see the bottom lip.

Here you can see the top lip, as well as all the rust that builds up and get in the fuel system.

Straighten the top lip out with a dolley and hammer, so it will lay flat when you weld it back together.

Blast the top and bottom pieces of the tank in and out.


The pin holes are hard to see, using a flash light behind helps locate them.


Do all your spot welding on the inside of the tank using a copper backing plate, this will save alot of grinding later.

Grind of the weld penatration the pops threw the sheet metal.


Dolley and hammer all the dents out.


Fit the Halves together.
Use vise grips to keep the sheets tight for welding.
Start at one corner and work around all four sides.
This allows you to tweek the grove back into the same location.
Tack weld about every three inches.
Grind all the tacks smooth so the seal weld can pass over them nicely.

Set the tank up on a 45 degree angle so the seam can be re-welded in a down hand position.

When welding ensure that the puddle fuses the sheet metal on both sides of the zip cut grove.
Use a slight whipping motion with the arc, backing up about 1/8" this lets you fix the weld puddle if it you loose the sheet metal on one side.
Repeat this welding on all four sides.

Here you can see the weld penatration on the back side of the seam.
Grind up any welds.

Use a polymer fuel tank liner to seal the entire interor of the tank.
This prevents rust from forming inside the tank and getting into the fuel system.
Tape up the openings.

Pour the polymer liner into the tank.

Tape the last opening and slowly rotate the tank.

Use a flash light to see that the entire interior of the tank is coated.
Pour the excess polymer out of the tank.
Let dry for 24 hrs

Paint the exterior of the tank with 2 coats of epoxy paint.
Reinstall the sending unit, vent plug and nozzle gasket.
Last edited by a moderator: