Hey guys. Had a question about trying to change the arch of the hood for a better fit. I am installing a dynacorn Hood on this 71 and got all my gaps pretty nice but it has way too much arch in the center and doesn't match the fenders for ****. I have quite a few shims under the centers of the fender but I cant really make them arch more. My question to you fellas is, how did you de-arch your hoods?? Seems like dynacorn cant get their **** together on these arches. I fit the hood and it looked decent but the arch is really bothering me. Unfortunately I didn't get a pic of it on the car. I was thinking of going a little cave man on the hood and laying it on some cardboard on the floor in garage and taking a 2x4 down the length of each side and pressing down and try to get the hood arch to relax a bit. Any other suggestions??
image hosting cdn
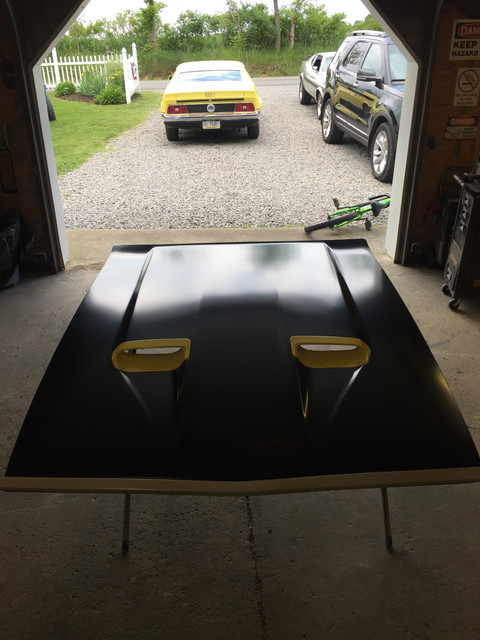
image hosting cdn
Last edited by a moderator: