iceberg65
Well-known member
- Joined
- Apr 9, 2016
- Messages
- 121
- Reaction score
- 1
- Location
- Medicine Hat, AB
- My Car
- 72 mustang Mach 1
351c 4v auto
Purists beware;
I retrofitted my inexpensive aftermarket tach inside my stock cluster. I just did not like the column mount for it especially having another tach right behind it. I already had almost everything apart so I thought I'd give it a go and it fit good enough that I can deal with it for a while like this. I do want to get the oem one rebuilt with modern guts so it can run off the square wave signal off my ignition but at this time there are more important things to put the money towards; plus the way I did this is easily reversed.
The fitment worked reasonably well; the tach is secured with a screw at the back that holds it against a piece of hardboard that I cut to fit snuggle inside the recesses where the stock tach sat. Its also held in by the factory screws. There is adhesive foam underneath it to give support; as well as at the bottom of the cluster to fill the gap it left. I hot glued the brake indicator lens to the front of the housing to maintain it's functionality with strips around it as well; I will however loose my brights indicator for the time being. With the way it's supported it sits quite solidly and doesn't move around at all being jostled about.
It's not great but it's functional and out of the way.
I retrofitted my inexpensive aftermarket tach inside my stock cluster. I just did not like the column mount for it especially having another tach right behind it. I already had almost everything apart so I thought I'd give it a go and it fit good enough that I can deal with it for a while like this. I do want to get the oem one rebuilt with modern guts so it can run off the square wave signal off my ignition but at this time there are more important things to put the money towards; plus the way I did this is easily reversed.
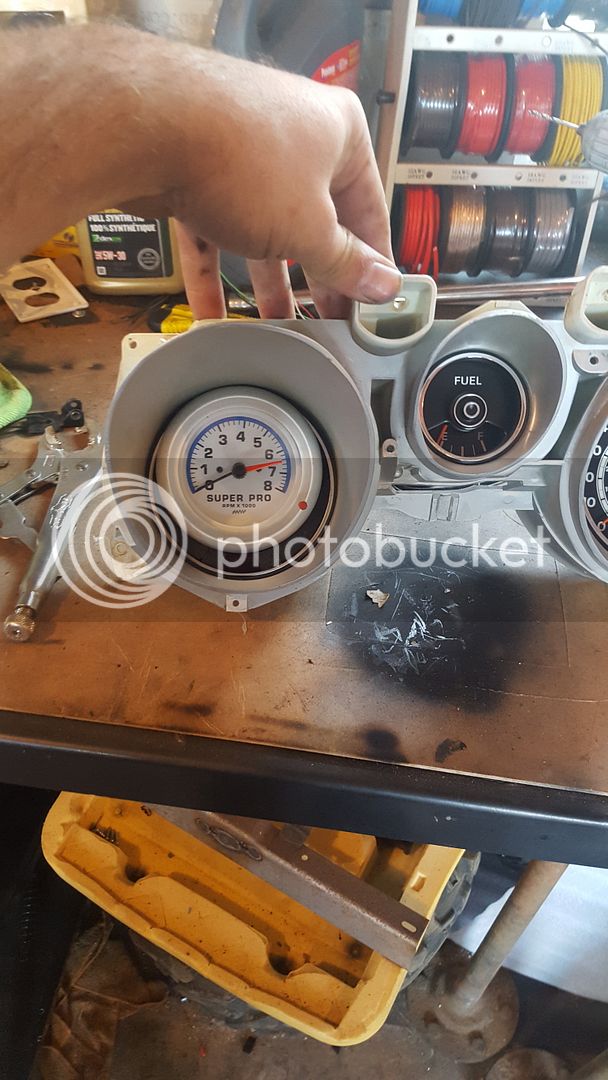
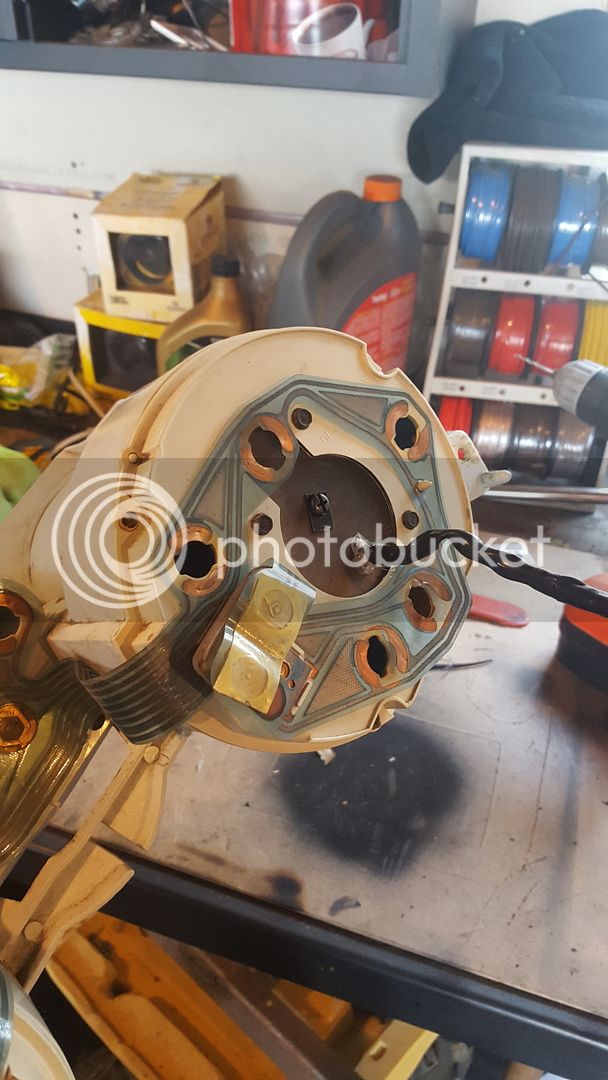
The fitment worked reasonably well; the tach is secured with a screw at the back that holds it against a piece of hardboard that I cut to fit snuggle inside the recesses where the stock tach sat. Its also held in by the factory screws. There is adhesive foam underneath it to give support; as well as at the bottom of the cluster to fill the gap it left. I hot glued the brake indicator lens to the front of the housing to maintain it's functionality with strips around it as well; I will however loose my brights indicator for the time being. With the way it's supported it sits quite solidly and doesn't move around at all being jostled about.
It's not great but it's functional and out of the way.