machattack
Well-known member
- Joined
- Apr 27, 2019
- Messages
- 705
- Reaction score
- 257
- Location
- Idaho
- My Car
- 1971 mustang mach 1 351c 4v auto fmx
1968 mustang gt 302 4v 4 speed
Can you folks take a look and tell me what you think is going on here?
I know its the solder joint ,both sides doing this. I replaced the whole rear of the car. Trunk pan, tail panel, trunk drops, inner wheel wells etc. The ripples were there prior to me replacing all the rear stuff. Nothing shifted, buckled or bowed in the repair process.
Some folks say the car was dropped off a tow truck. Others say the car has been jumped.
I remember a thread that I think Carolina mustang said it was none of these things? but I cant remember what his answer was......cant find that thread either and Im exhausted looking for it.
I know its the solder joint ,both sides doing this. I replaced the whole rear of the car. Trunk pan, tail panel, trunk drops, inner wheel wells etc. The ripples were there prior to me replacing all the rear stuff. Nothing shifted, buckled or bowed in the repair process.
Some folks say the car was dropped off a tow truck. Others say the car has been jumped.
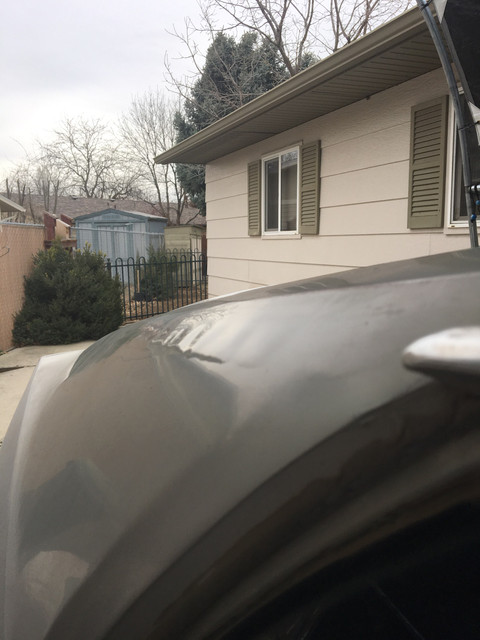